To keep a community’s traffic moving smoothly, roadways must be thoroughly maintained to remove debris and litter from the roads, ensure proper stormwater management along the corridors, preserve the infrastructure, and protect travelers against harsh weather conditions.
Maintenance facilities are placed in strategic locations along highways to provide ease of access to the resources needed to address these types of concerns within a transportation network. In the summer of 2020, the Prince George’s County Department of Public Works and Transportation began the construction of a state-of-the-art highway maintenance facility in Brandywine, Maryland, to replace a deficient storage yard and to expand the resources and responsiveness of County services. KCI was contracted to provide construction management and inspection services for the new construction of several buildings on the site.
The new project site location was a critical element in the Department’s Snow Operation plan, making it essential that the facility and its resources be in place prior to the start of the winter weather season. After the existing facility was demolished, innovative solutions using remote and digital technologies allowed KCI to accelerate the schedule for delivering the new 10,000-ton capacity salt barn and its associated site access points. Experienced in working for the County directly, KCI had an intimate knowledge of the facility’s importance and urgency that was required to keep the project moving forward on the tight 12-month schedule. This experience, in addition to innovative techniques and open communication, allowed our team to address any concerns that arose throughout the project’s duration.
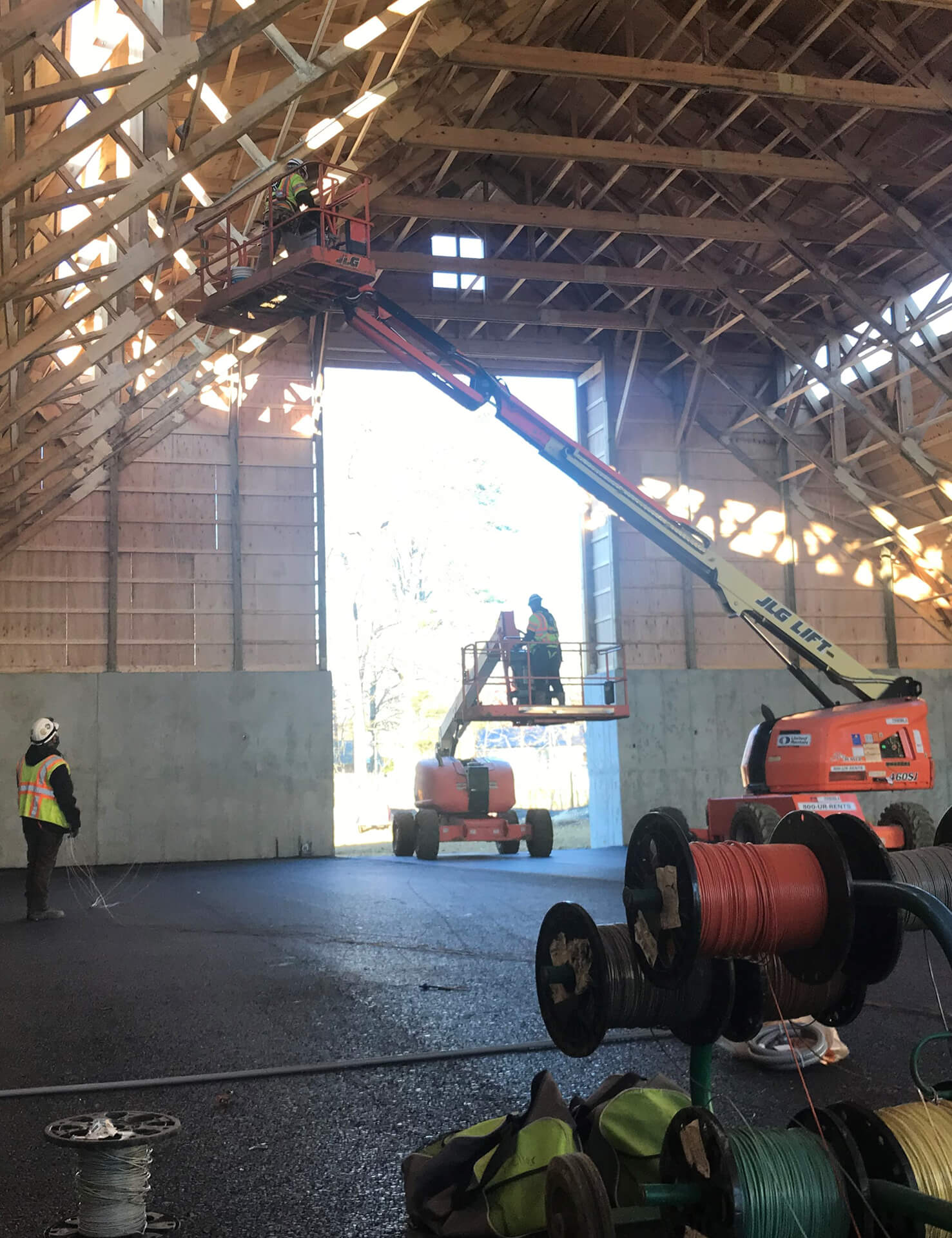
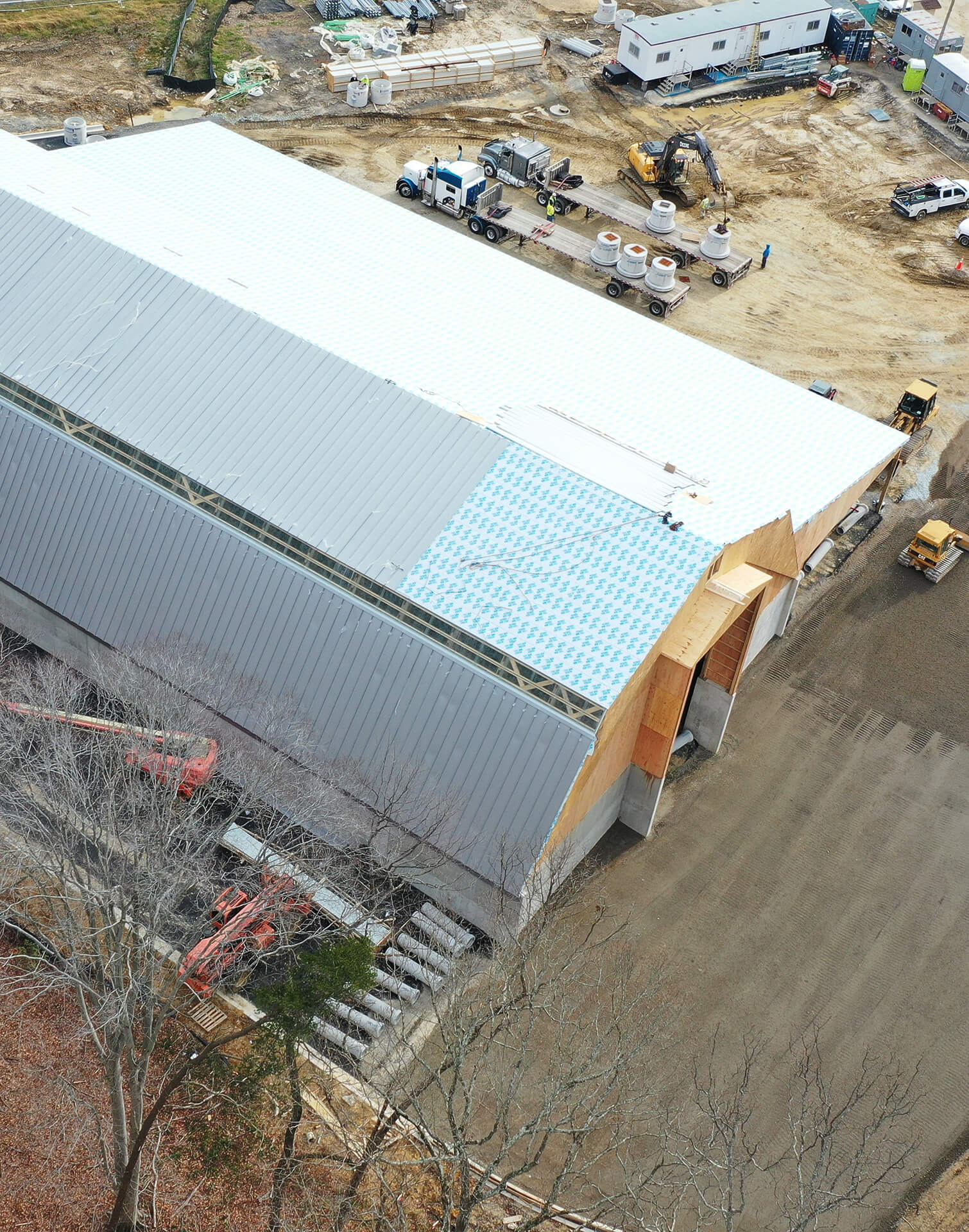
Following the demolition of the existing facility, potential issues with soil conditions were quickly recognized and pockets of unsuitable materials were discovered along the site. KCI’s construction staff was able to overcome these challenges by creating a soils management plan that established a course of action for site conditions as they were met, outlining the limits of removal and replacement based on the site conditions and the location within the project site. This plan provided clear technical guidance for all parties involved to collectively enact a solution while also controlling costs.
“KCI strives to take the role of partner for any job. We are there to solve problems and facilitate a successful outcome for all of our clients, and the entire team worked together to ensure the new Brandywine maintenance facility would also be successful.”
– James Wilson, PE, Practice Leader
Throughout the project timeline, which occurred during the height of the pandemic, KCI prioritized open communication and partnering between all stakeholders to ensure a smooth project delivery. Our team kept things on track safely by hosting meetings to discuss potential changes and overall contract administration remotely and observing all local and federal COVID-19 procedures onsite. Through the use of KCI’s in-house e-construction application, Mobile Field Services, our team was able to digitize reports to stay connected while reducing the amount of on-site personnel. The team’s project managers oversaw daily activities through electronic records that digitized Inspector Daily Reports used to document construction progress, helping the Brandywine team expedite workflows, standardize data collection, and improve quality control. Information was captured for workload and staffing, planned versus completed tasks, manpower on-site, and other data based on the requirements of the inspector’s assigned task. This aggregated data allowed the team to develop reports that tabulated inspections, item summaries and contractor lists on demand while providing field inspectors with real-time updates on any contract data.
In addition to digital reporting and data collection, the use of unmanned aerial vehicles allowed our staff to conduct project site surveys without close physical contact between team members. Prior to the start of the project, a preliminary drone flight captured the initial state of the site for construction monitoring. As the project progressed, KCI’s inhouse drone pilot regularly returned to the site to document biweekly updates. Our team provided video flythroughs, panoramic images and a full map scan, in addition to recording changes to the overall landscape as the facility was built and making note of detailed aspects such as the condition of the newly constructed building’s roof. After the County received the visual report and shared it with key stakeholders, the contractor team was made aware of adjustments at an accelerated rate. The video footage was also readily available to extend to the public, enabling the County to keep the local community informed with digital outreach efforts.
With the importance of creating a sustainable environment in mind, bioretention facilities were added to the design and utilizing the soil management plan allowed our team to rectify environmental issues in the ground prior to construction. The overall site was cleaned of major contaminants before substantial completion, and best management practices (BMPs) will help prevent pollutants originating from the construction site from reaching storm sewers. Electric vehicle charging stations were also installed at the facility to promote green transportation and allow the community’s transit leaders to utilize the site for their sustainable buses.
To keep the schedule moving, the project team held progress meetings every two weeks to review and ensure tasks were still on track. Contractors, engineers and the County were in continuous communication and collaborated to partner together and solve problems as a united front. Several times, our team was called upon to observe issues onsite and worked to quickly provide a solution within 24 hours. Throughout the process, KCI was also responsible for coordinating required third party inspections on behalf of the project team.
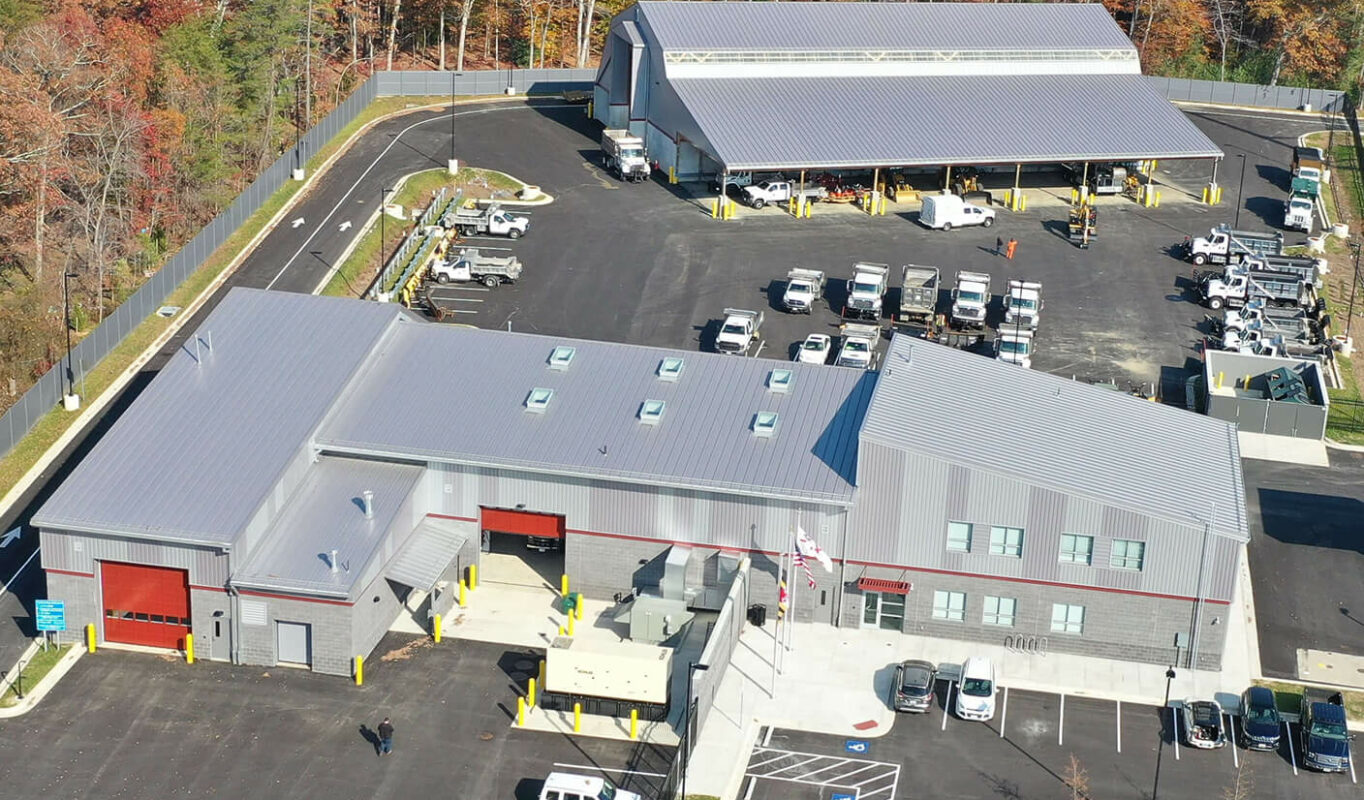
Thanks to the teamwork and coordination of everyone involved in the project, the maintenance facility and its adjacent salt barn were opened and ready for use by the County’s critical date. In recognition of the newly opened site’s sustainable design features, Vice President Kamala Harris visited the Brandywine facility shortly after its opening to tour the electric vehicle charging stations and announce the administration’s $7.5 billion plan to develop a nationwide electric vehicle infrastructure system. KCI, Prince George’s County, and contractors worked together seamlessly to provide this new, state-of-the-art facility that will allow crews access to the resources needed to keep Prince George’s County’s residents and commuters safely on the roads.